Certified B Corporation + Sustainability Efforts
On Earth Day, 2020, we were thrilled to announce that Lakefront Brewery has achieved Certified B Corporation status. We are the very first brewery in Wisconsin and just the 22nd brewery in the world to be certified. Certified B Corporations are businesses that meet the highest standards of verified social and environmental performance, public transparency, and legal accountability to balance profit and purpose. For more information about Certified B Corporations, visit https://bcorporation.net
We here at Lakefront Brewery know the importance of supporting local communities. That’s why, at the end of your tour, you receive a coupon for a free pint at several local establishments. We love that you’ve come to visit us, but we want you to explore and enjoy even more of Milwaukee’s gemütlichkeit (warmth, friendliness and good cheer).
View Lakefront Brewery’s Certified B Corporation 2020 Impact Report (PDF), 2021 Impact Report (PDF), 2022 Impact Report (PDF), 2023 Impact Report (PDF), and 2024 Impact Report (PDF).
1980s & 1990s
- We bought a building built on a brown field that was remediated. The brewery also has a white roof, which reduces heat absorption and reflects up to 90% of sunlight. A white roof also reduces ambient temperature around a structure and reduces the “urban heat island” effect.
- In 1996, we became the country’s first certified-organic brewery.
- In 1997, we began using a heat exchanger with our boil to reuse hot water.
- In 1999, we began using a setback thermostat in the Beer Hall.
2000s
- In 2001, we purchased and installed the Bernie Brewer Chalet from the former County Stadium.
- In 2005, we partnered with Growing Power to supply them with spent grain. We also began to purchase perch from Growing Power for our fish fries.
- In 2006, our president, Russ Klisch, became a founding member and vice president of Local First Milwaukee, an advocacy group concerned with folks buying local.
- In 2007, we became the first Travel Green brewery in the state. We were also recognized for sustainable practices by the Wisconsin Department of Natural Resources’ Green Tier program.
- In 2008–2009, we:
- Replaced our exit lights with LED exit signs
- Swapped tour cups with 100% plant-based cups
- Began printing all printed material on recycled paper with soy ink
- Began making 6-pack carriers with recycled paper stock
2010
- We installed a thermistor on the fridge to pre-heat water.
2011
- All lighting in the brewhouse was replaced with energy efficient lighting
- We installed a heat-recovery unit to use waste heat from refrigeration to preheat water, which is used for tank cleaning as well as building hot water service.
- We installed pressure switches on condenser fans to run independently. This reduces electricity use by half when only one fan is needed.
- We installed new glycol service loops with pressure-controlled variable frequency drives on the pump motors, reducing the electricity use when fewer tanks demand cooling. Multiple service loops for the glycol system were combined into larger systems that run more efficiently.
- We were awarded a grant from the Wisconsin Profitability and Sustainability Initiative used for:
- Tying refrigeration systems into the heat recovery unit
- Upgrading the single-stage wort exchanger with a larger two-stage model that will decrease our water usage and total load on the glycol refrigeration system in the summer months
- Developing a database to monitor electricity, natural gas, and water use efficiencies compared to beer sales
- We removed a redundant cold storage room and shut down its refrigeration unit to save electricity.
- We switched from stretch wrap to poly strap for keg palletization. Poly strap is recyclable and uses less material.
- We switched to a new bottle type that uses less glass for the same volume container.
- We installed a gas blending system for the bar beer draft system resulting in less gas wasted and fewer bottle deliveries for decreases in fuel consumption.
- We brewed the first gluten-free beer (and changed the government’s policy and definition of beer).
2013
- We installed Dyson hand dryers in restrooms to reduce paper use.
- We use CHEP pallets, which are leased. Pallets are repaired—not thrown out. Odd-sized pallets have the nails removed and are recycled. The wood is ground for animal bedding.
- We purchased a machine to compact stretch wrap.
- We began selling our OCC (old corrugated cardboard).
- We brewed “Local Acre Wet Hop” beer using only local ingredient beer.
- Our beers “My Turn Luther” and “Wisconsinite” won Good Food awards.
- We supplied barrels to KHS USA to be packed with school and medical supplies, toys for kids, clothing, and tools for wood carvers in Jamaica.
- We held a recycling event with 5R Processors Ltd. to recycle electronic devices. We also installed a second thermistor on the fridge to pre-heat water.
2014
- We earned 150 points to qualify for the Green Master’s Program certificate.
- We landscaped with native and/or drought-resistant plants.
- We began using permeable surfaces where possible.
- Our beer “Wisconsinite” won another Good Food award.
- We sent a letter to the EPA Administrator Gina McCarthy in support of the EPA draft rule “Definition of Water of the United States Under the Clean Water Act,” which advocated for clean water protection. We donated 37 barrels to Wellspring Education Center and Organic Farm.
- We began using Microstar kegs, which dramatically reduce carbon emissions by sharing kegs). Microstar is part of the EPA’s SmartWay Program committing to further track and reduce transportation-related emissions and fuel use.
2015
- We installed motion lights in our liquor room to avoid the lights being left on.
- Instead of using a continuous rinse, we began using a stainless drum, which is filled with 65 gallons of water, 650 ml of oxine, and 5 ml phosphoric acid usually twice-a-day, reducing the usage of water to 132 gallons of water instead of gallons per minute.
- We automated our bottle wash to turn on only when bottles are running through it instead of a continuous flow.
- We began brewing “Growing Power” organic beer. Our beer “Organic Belgian White” won a Good Food award.
2016
- We installed new front door and garage doors with improved weather stripping.
- We contracted with Compost Crusader to recycle organic waste. Through the Dumpster for Dirt Program, for every 20,000 lbs. of material Compost Crusaders diverts from the landfill, one yard of finished compost will be donated back to the community. Lakefront will send between 4,100-4,985 lbs.
- We began running cooling during off peak hours.
- Our beer “Growing Power” won a Good Food Award.
- We installed a timer for the rinse cycle in the whirlpool that prevents the overuse of hot water.
- We installed water-sense toilets in the women’s room.
2017
- We installed a 70KWdc solar roof top system on our warehouse to offset approximately 39% of current annual energy consumption for the electrical grid.
- There was 14.34 MWh produced from solar panels.
- Our beer “Fuel Café Coffee Stout” won a Good Food Award.
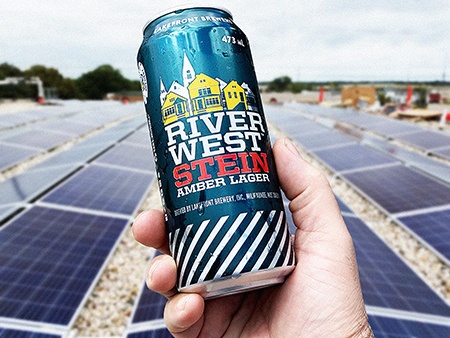
2018
- Our beer “Latif Double Chocolate Stout” won a Good Food Award.
- There was 78.77 MWh produced from solar panels.
- President Russ Klisch offered to supply Uber/Lyft ride for employees who have to walk home alone at night.
2019
- We obtained Lake Friendly Certification.
- Our beer “Fuel Café Coffee Stout” won a Good Food Award.
- We attended Quad Graphics (vendor) Sustainability Symposium.
- We donated $.50 from every tap beer to Drink Local, Think Global.
- There was 72.94MWh produced from solar panels.
- Over 56 tons of C02 was reduced from solar panel use in 2019.
- We conducted a food drive for Hunger Task Force during our Black Friday event.
- We conducted a coat drive for One Warm Coat.
- We conducted a toy drive for Toys for Tots.
- 5% of food and drink sales, for a given day, were donated to Milwaukee High School of the Arts and Carver Academy.
- We donated $1 per pint to the Wisconsin Bike Fed during the Santa Rampage bike ride.
- We hosted Food Fright for Local First Milwaukee, donating 100% of ticket sales to Local First Milwaukee.
- We hosted Keg Stand Up comedy night with all female comedians and donated $1 per pint to Riverwest FemFest.
- We created a rain garden on our property. We have 53 plants that each takes in a gallon of runoff water a day April-August slowly infiltrating it into the ground which is an excellent means of removing pollutants.
- Each rubber coaster in the gift shop keeps approximately 1.6 oz. of rubber out of the landfill and 1.6 oz. of crude oil from being consumed.
- All of our packing material is either reused to ship out gift shop items or recycled at UPS.
- The large chandeliers hanging in the Beer Hall were recovered from the 1916 Plankinton Hotel.
- We give an environmental tour each Friday at 4 pm.
- We offer a “Bikes and Busses” discount on a customer’s first beer or brewery tour if they choose a more sustainable mode of transportation.
2020
- Joined Bicycle Benefits Program to support biking to the brewery.
- Lab was completely gutted and fit with new lab-quality shelves and counters.
- Bushfire Relief Week- Discounts on Riverwest Stein and IPA and donated all proceeds (Feb 23-Feb 29) as part of #FlagshipFebruary to Australian Resilience Fundraiser.
- Brought back Wisconsinite, a fully local beer.
- Won Good Food Award in San Francisco for the 2020 Beerline Barleywine (2021)
- Lakefront Brewery adopted the portion of the river from Pleasant St. to Humboldt Ave. to do our part: employees pick up trash along this route.
- Six-pack give away to health care providers in April; over 3,300 six-packs given out.
- Painted Brewery internal walls; installed new drains by bright tanks, epoxied the floor by the bright tanks, fixed the drain by the end of the ramp in packaging
- Beer Hall received new epoxy floor in kitchen with drain, new epoxy ramp entering the gift shop, epoxied behind bar.
- New sink in the upstairs men’s bathroom with motion activated faucet
- New Beer lines behind the bar, increased from 12 faucets to 18 faucets; new soda lines which improved cleaning behind the bar. Hand wash sink and new three-compartment sink installed. New serving glass washer installed.
- Installed blinds on the river side of the beer hall reducing heat in the summer, maintaining heat in winter
- Three days of BloodCenterWI Blood Drive (Free coupon for a pint of beer)
- Annual Make and Paint Your Own Rain Barrel event cancelled, but managed to partner with Milwaukee Riverkeeper to sell 24 Barrels with kits (painting will just have to be done at home…)
- COVID safety plan approved by the city for in-person dining without capacity limits. Social distancing still applied.
- Doors Open virtual 360 tour of the brewery.
- Voter registration at the Beer Hall October 2020.
- Created “Hop Houses” on the Riverwalk for private, outside dining which will later be converted into green houses during the warmer months.
- American Red Cross blood drive on November 10 (All participants receive a bottle of beer or root beer and a $5 amazon gift card).
- Participated in Riverkeepers, working for swimmable, fishable rivers throughout the Milwaukee River Basin.
- Fall cleanup Commerce St between Pleasant and Humboldt (gloves and bags provided).
- Joined NRDC Brewers for Clean Water.
2021
- Valentine’s Day Mass Vow renewals were performed over Zoom to maintain social distancing.
- Blood Drives scheduled at the brewery (26 units of blood collected at the first drive–which will impact nearly 80 local lives).
- March 8th Pink Boots Brew Day at Lakefront Brewery with women from Malteurop, 15 bbl batch -Donated $500 to Pink Boots Society for Sales of Pink Boots Pale Ale 9/2/2021.
- Employees volunteered April 15-24 to pick up trash from Pleasant to Humboldt bridge clean to keep the trash from ending up in the river.
- Hosted Dreambikes at the Beer Hall to collect donations of used bikes.
- Brewed Lakefront Brewery’s very first Non-Alcoholic Beer, Riverwest Stein NA.
- May 20th American Cancer Society Benefit at the Drunk Uncle: 100% of proceeds from draft pours of My Turn: Al were donated.
- Lieutenant Governor Mandela Barnes came to visit; Russ gave a tour of the Brewery including some sustainable projects.
- Milwaukee Riverkeepers and students from St. Robert’s grade school in Shorewood primed the barrels before our annual rain barrel day on September 27th; picked up garbage along the Riverwalk.
- Joined Great Lakes Business Network (2021).
- Wisconsin Humane Society with Lakefront Brewery and other breweries to support the animals for Brewery Give Back Day. Portion of our beer sales went to provide food, shelter and lifesaving medical care to animals in need in the Milwaukee area.
- Rising Hope IPA brewed and sold in the Beer Hall with a portion of the proceeds donated to the National Pediatric Cancer Society.
- Supported Brew City Beer Pass from VISIT Milwaukee (BOGO beer).
- New water dispenser at Warehouse 8/31/2021. Energy Efficient replacing old bubbler. In line rather than bottle; saving money and plastic.
- Pint for Poke Tuesday, September 7, 4–9PM Adults 21+ who show their COVID-10 vaccination card or who get their shot at the event received a token for a free beer. With Opportunity Wisconsin & amiexphealth.
- Live Again Initiative by Milwaukee-area beverage makers to support re-emergence of local independent venues after the long silence of COVID-19.
- Given Green Professional Designation from the Green Masters Program with a score of 303 across 9 categories (energy, carbon/greenhouse gases, water, waste management, transportation, supply chain, education and outreach, workforce and governance).
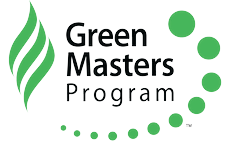
2022
- Mobile Blood Drive Jan 13th, 2022
- Good Food Award for Wisconsinite Weiss
- Inaugural Milwaukee Mayoral Firkin Tapping January 29th during My Turn: Tyler party at Black Husky Brewing (All 7 Milwaukee Mayoral special election candidates together for a cordial mass beer firkin tapping Saturday, January 29th- all proceeds from $5 firkin pours will benefit the upkeep of the River Revitalization Foundation’s Turtle Park.)
- Letting Victory Garden Initiative use Lakefront Trailer for Victory Garden Initiative Blitz
- Joined WSBC (WI Sustainable Business Council).
- New water heater at warehouse.
- Sponsored Run 4 Water (UWM/ Engineers without borders).
PROUD PARTNERS
We’ve got friends – friends who are excellent business partners.
Please recognize these companies and if you have a chance to do business with them, please join us. Cheers.
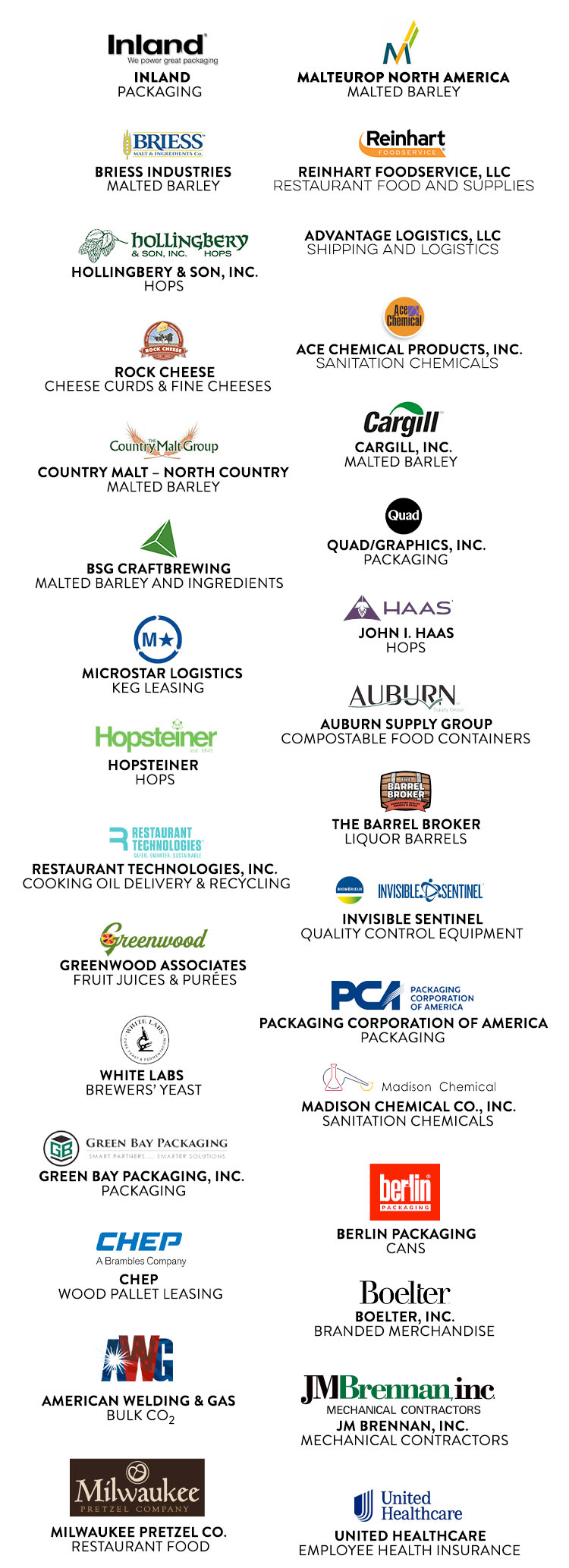